Manganese vs Zinc Phosphate Coatings
Phosphate coatings play a key role in protecting metal parts, making them last longer and perform better. These coatings form a protective layer that improves corrosion resistance, reduces friction, and helps other finishes stick to the surface.
Industries such as automotive, aerospace, firearms, and heavy equipment manufacturing depend on phosphate coatings to strengthen metal components. But while both zinc phosphate and manganese phosphate offer protection, they serve different purposes.
At Light Metals Coloring, we specialize in manganese phosphate coatings, which are particularly useful for high-friction applications. While zinc phosphate has its place in some industries, LMC does not provide this coating. Here, we’ll break down the differences so you can decide which is right for your needs.
What Are Phosphate Coatings?
Phosphate coatings are created through a chemical treatment process using phosphoric acid to change the surface of the metal. This textured, crystalline layer provides three main benefits:
Corrosion Protection – Shields metal from rust and environmental damage.
Lubrication – Reduces wear and friction, extending the lifespan of moving parts.
Better Adhesion – Prepares the surface for paint, lubricants, or sealants to stick more effectively.
These advantages make phosphate coatings a top choice for industries that require long-lasting metal components.
Zinc Phosphate Coatings
What Is Zinc Phosphate Coating?
Zinc phosphate is a thin, crystalline coating applied through an immersion process. This type of coating is best known for its ability to help paint and sealants adhere, making it a common choice in automotive and military applications.
The treatment process involves immersing the metal in a phosphoric acid solution, which creates a fine-textured surface. While zinc phosphate provides some corrosion resistance, it usually requires an additional sealant or oil coating to perform best in harsh environments.
Key Benefits & Applications
Zinc phosphate is widely used when a strong base for paint or primer is required. It is also valued for its moderate corrosion protection, though it often needs an extra layer of protection for long-term durability.
Industries that commonly use zinc phosphate coatings include:
Automotive – Applied to car frames, underbodies, and other components before painting.
Military Equipment – Protects metal surfaces from rust and damage.
General Industrial Use – Provides a solid foundation for coatings in manufacturing processes.
Although zinc phosphate is useful in these areas, LMC focuses solely on manganese phosphate coatings that offer greater wear resistance and lubrication.
Manganese Phosphate Coatings
What Is Manganese Phosphate Coating?
Manganese phosphate coatings create a thicker, more durable layer than zinc phosphate. This makes them ideal for high-wear applications where friction and movement could cause uncoated metal to degrade quickly.
One of the biggest advantages of manganese phosphate is its ability to hold oil and lubricants, allowing metal components to move smoothly and resist wear over time. Because of this, it is commonly used in firearms, gears, camshafts, and heavy machinery.
Key Benefits & Applications
Manganese phosphate coatings are designed to withstand heavy friction and mechanical stress. Their ability to retain oil makes them the preferred choice for applications where metal-on-metal contact is frequent.
Some common uses of manganese phosphate include -
Firearms Manufacturing – Used to coat barrels, bolts, and other parts to improve durability.
Automotive & Machinery – Helps reduce wear on gears, camshafts, and other moving parts.
Industrial Equipment – Protects machine components that operate under continuous stress.
If a tough, long-lasting coating is needed to reduce friction and extend the lifespan of parts, manganese phosphate is the best option.
Comparing Zinc and Manganese Phosphate Coatings
If you're deciding between zinc and manganese phosphate, it's important to understand how they differ:
Feature | Zinc Phosphate | Manganese Phosphate |
---|---|---|
Corrosion Resistance | Moderate (better with paint/sealant) | Good (when combined with oil) |
Wear Resistance | Low | High |
Lubricity | Moderate | Excellent |
Best For | Paint adhesion, corrosion resistance | High-friction, high-wear applications |
Common Applications | Automotive, military, industrial | Firearms, heavy machinery, gears |
If your project requires a strong primer base for paint or moderate corrosion resistance, zinc phosphate may be suitable. However, if you need high durability, friction reduction, and long-lasting protection, manganese phosphate is the better choice.
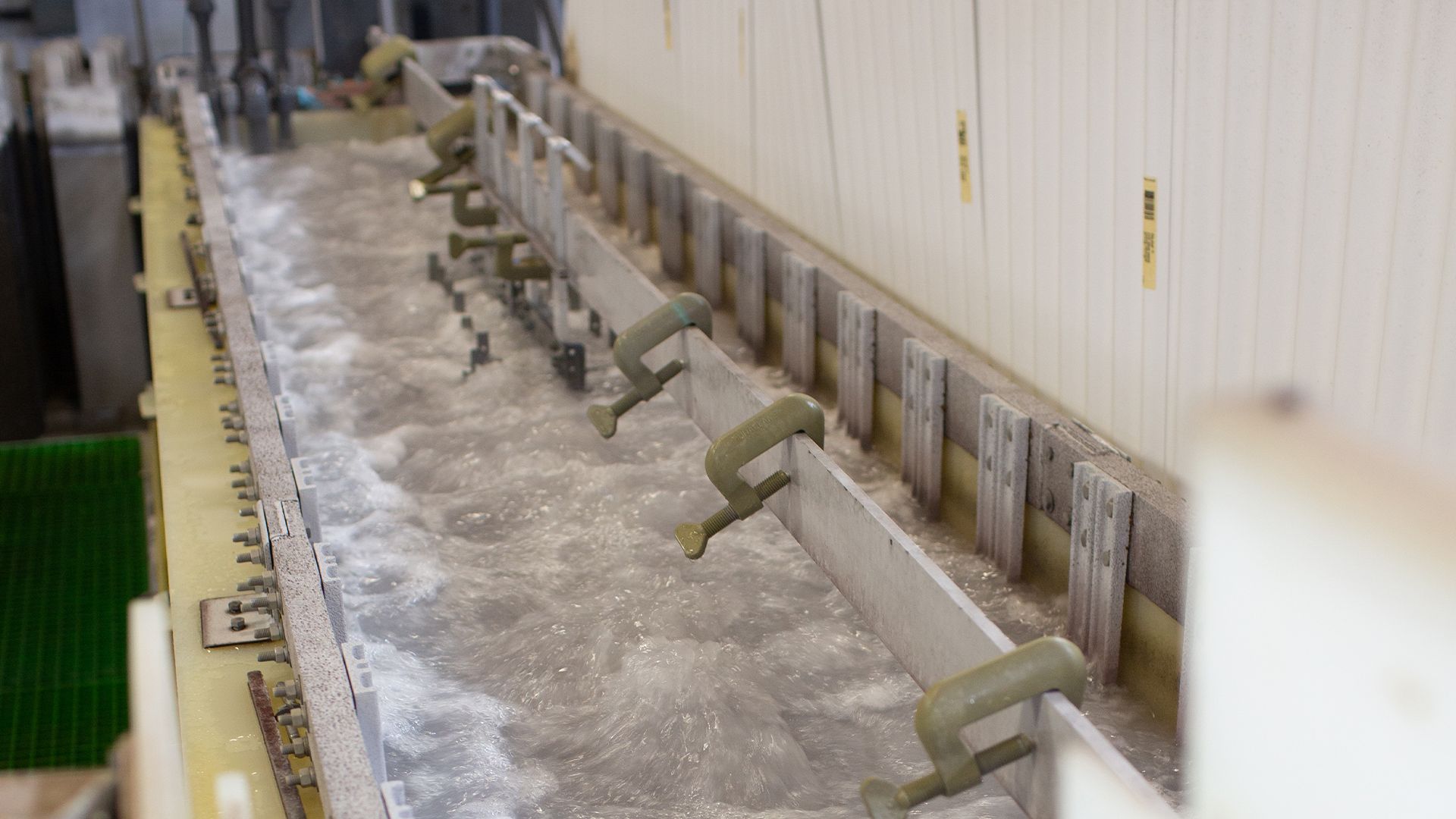
Choosing the Right Phosphate Coating
To select the best phosphate coating, consider the following factors:
Exposure Conditions – Will the component face moisture, chemicals, or extreme temperatures?
Wear & Friction – Does the part need to withstand constant movement and stress?
Intended Use – Is the coating meant for paint adhesion, corrosion protection, or reducing friction?
When Zinc Phosphate Is a Good Fit
If your main goal is paint adhesion and moderate corrosion resistance, zinc phosphate is often used as a primer base. Keep in mind that it may require additional sealants to provide long-term protection in demanding environments.
When Manganese Phosphate Is the Better Choice
Manganese phosphate is the preferred option when high wear resistance and strong lubrication retention are essential. If your components are under constant friction or heavy stress, this coating will provide the most effective protection (especially when paired with oil treatments).
Making the Right Choice for Your Needs
Both zinc and manganese phosphate coatings serve valuable purposes, but they excel in different areas. Zinc phosphate is primarily used for paint adhesion and moderate corrosion resistance, while manganese phosphate is ideal for reducing wear and improving lubrication in high-friction applications.
At LMC, we specialize in manganese phosphate coatings to help extend the life of your metal components. If you need guidance on the best coating for your project, contact LMC today for expert recommendations and high-quality metal finishing solutions.